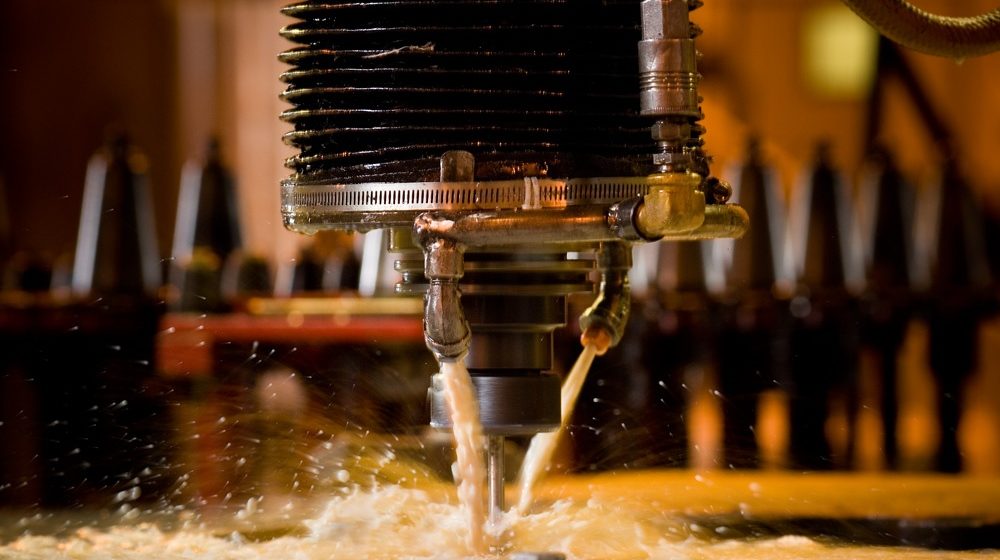
Why Precision Manufacturing is More Than A Fad
July 31, 2018
Management theory is full of fads – remember business process re-engineering or matrix management? While these fads start off with good intentions, a hallmark of a management fad is that the program (often being sold by consultants) has little in common with the original approach. As such, results may be missed and, in many cases, organizations go back to the way things were done before.
But the movement towards “precision manufacturing” might be different. For starters, it is driven by advances in software, communications technology, and materials. Add in the fact that many see it as an opportunity for domestic OEMs to remain competitive in a global market, and you’ve got yourself a new standard.
Let’s review the basis that’s pushing precision manufacturing beyond just a trend.
What is Precision Manufacturing?
You know it by many names – Industry 4.0, smart factories, advanced manufacturing, or precision manufacturing. While we could delve into the semantics of these terms, it is better to focus on the application. This involves the techniques and methods used in the design and production of essential hardware, parts, and tools used today. These methods enable manufacturers to reach tighter tolerances at a higher level of process control compared to just 20 years ago.
While this might lead one to think that precision manufacturing is only used to make smaller items, the reality is that the underlying processes can be applied to almost anything. For this reason, leading steel fabricators in the U.S. have transitioned to a precision manufacturing ecosystem.
Beyond increased process control, precision manufacturing also allows for a heightened level of traceability required by industries from medical devices to automotive parts and assemblies.
Precision manufacturing is not the destination; it is a continuous process of improvement and integration. While the reasons a strategic partner would choose to invest in precision manufacturing vary, the results are one reason why many in the U.S. have been able to remain competitive in a global economy.
This improved value, in terms of quality, cost, and lead time, has also helped OEMs to reshore much of the work they moved to factories in Asia and elsewhere not so long ago. As such, one can say that precision manufacturing is not a fad – it is the future of manufacturing in the U.S.
What are the drivers behind precision manufacturing? Research has identified three which, when properly integrated into production and supply chains, can give OEMs a tangible advantage over the competition.
Advantage 1: Advanced Software
Compare the production floor of many metal fabricators today to one even in the 1990s and you will be amazed by the transformation. Sure, lean manufacturing has long since taken hold and strategic partners have embraced approaches, such as one-piece flow and just in time deliveries. But the real change is that technology has made its way into manufacturing.One example is the advanced analytics available to metal fabrication partners and their OEM customers. These tools allow supply chain managers and production engineers to make decisions about material selection, scheduling, cost, and even redesigns in near real time. In addition, fabricators have the capability to upload designs straight from CAD files to the machines tasked with processing the part, thus eliminating operator error.
Advantage 2: Manufacturing as a Service (MaaS)
While outsourcing has always been a key element of MaaS, it has traditionally been a high-touch process requiring hundreds, if not thousands, of hours from engineers and supply chain professionals to deliver results.
But precision manufacturing is beginning to change this. Gone are the days of weeks-long junkets to Asia to visit suppliers, as they are replaced with continuous communications with partners on everything from material decisions to pricing to delivery dates. However, the real breakthrough is how design has become a collaborative process, with strategic partners providing the insight needed to build better products in the prototype stage.
Beyond this, some partners are even beginning to co-locate all or part of their production within the facilities of their customers. While this is still rare, it illustrates the shift in mindset within manufacturing leaders as they try to tie up OEM accounts for years to come.
Advantage 3: Lead Times
One drawback to manufacturing in Asia is the time it takes to get the product from the factory to market – even when the fabrication partner is using advanced practices. The reason is simple, making all or part of an assembly in one market and then shipping it to another market results in lost time and energy.
As such, many OEMs have begun to rethink their manufacturing strategies. Sure, some components and sub-assemblies will continue to be made in low-cost countries and then shipped to global markets. However, the added lead times mean that moving even part of the production process back into the market can help the OEM save millions in supply chain costs.
This is especially true when it comes to precision parts manufacturing, as having a partner in the market can reduce the lead time from weeks to 3 days, or in some cases, less. Not only does this give an OEM a time advantage, but it also allows for a more collaborative approach to process improvement.
A Fundamental Change
While a future where the manufacture of physical products will be completely automated is still some ways off, there is no doubting that we are moving in that direction. The processes and technologies which enable precision manufacturing are very real and are being actively employed by leading fabrication partners.
This is not a management fad; it is a fundamental change in how we make the machines which have made the modern world. Regardless of your industry, if you want to remain competitive, you need to integrate these approaches into your production – whether it is internal or via your strategic fabrication partner.
See the full list of equipment that Miller Fabrication Solutions uses to precision manufacture metal parts for global OEMs across the construction, oil & gas, mining and agricultural equipment, and material handling industries.