Total Solutions
Materials we use
Your custom metal parts fabrication projects can mandate the use of a number of metals, each having their own unique properties to manipulate during the fabrication process. Miller Fabrication Solutions has the deep expertise to work with a variety of metals to accommodate your specific metal part projects.
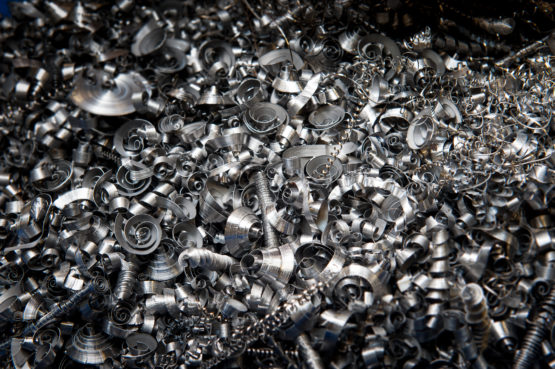