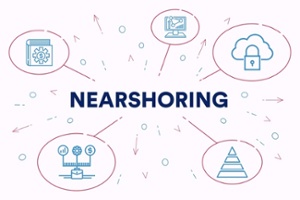
Nearshoring: The Real Impact of Technology in Manufacturing
April 4, 2018
Supply Chain Management is chock full of buzzwords. Elastic, enterprise mobility, cost to serve, and nearshoring are examples of the rush to embrace ‘silver bullet’ solutions for everything that keeps managers up at night. While there is always an element of truth to these buzzwords, the reality is that many of these phrases oversimplify the evolution of manufacturing.
For instance, nearshoring. The concept is easy to understand – moving manufacturing closer to the customer. This might mean taking ownership of a long-outsourced process from suppliers in Asia to in-house facilities, called ‘reshoring.’
Or it might mean shifting supply bases from halfway around the world to locations closer to home. While these processes are still outsourced, the move to bring manufacturing closer to one’s customers helps to reduce time and costs while allowing for a more responsive supply chain.
What is often overlooked in this is the role of technology in manufacturing – a key enabler in the nearshoring of complex supply chains. This helped manufacturers in the U.S. to survive by giving them a leg up by extending capabilities while keeping costs in check. With that in mind, here is what you need to know about nearshoring: the real impact of technology in manufacturing.
Down But Not Out
While widely reported, the ‘death of U.S. manufacturing’ is more nuanced than previously thought. Yes, the days of large-scale factories employing tens of thousands of workers have largely faded. But these massive and inefficient facilities have given way to a movement that is sparking a renaissance across the country – advanced manufacturing.
The shift has helped today’s manufacturing workers to produce more with less and is heavily reliant on rapidly maturing technologies such as robotics, automation, and analytics. Combined, they are transforming how factories look and function, making it possible to bring production back home while being cost competitive.
The Rise of the Machines
A lot has been made about the increasing role of automation in manufacturing. However, this is a trend that has been with us since the invention of the cotton gin. What is causing some observers to take notice is the speed of the change. For example, a recent analysis by the Brookings Institution estimated that there are close to 2 million robots deployed in factories and warehouses around the world.
These aren’t the welding robots of the 1970s, as today’s robots can do so much more. Furthermore, the costs of implementing these machines on the factory floor is falling rapidly. So much that the same report from Brookings estimated that in the U.S. the labor savings generated from automation alone is roughly 16 percent.
In fact, the savings are even higher in places like South Korea and Japan, and this is one reason why these countries have been able to withstand the never-ending onslaught of low-cost manufacturers from China and elsewhere.
The impact is that the trend of shifting manufacturing to low-cost countries halfway around the world is finally coming to an end. This might mean that you won’t have to deal with jet lag as a result of flying to Asia every quarter for supplier meetings, as more and more of your supplier partners will be operating in the same region as you. This will lead to a more agile and responsive supply chain – and ultimately lower costs and better quality.
What Does This Mean?
While advances in technology have helped to make nearshoring manufacturing possible, it is not a panacea. For starters, vendors must possess the capabilities needed to add value in this new environment.
This means having experienced analysts, engineers, and technicians who can collaborate over the entire life cycle of a product, leading to the holy grail of supply chain management – integration.
However, you need to know how to test if your metal fabrication partners can really deliver on this promise. If not, then all you have done is traded headaches half a world away for those closer to home.
As such, you want to start by understanding:
- The life cycle of your products;
- The benefit gained from rapid delivery windows;
- Customer demand, including predictability;
- Lastly, the causes, and impact, of variety.
By understanding these variables, you can better define what it is that you need in a custom fabricator. While this may seem daunting, doing so will help you to leverage the technological capabilities of your metal fabrication partners for the benefit of you and your customers.
To learn more about how the expanded capabilities provided by Miller Fabrication Solutions can add value, schedule a free consultation today.