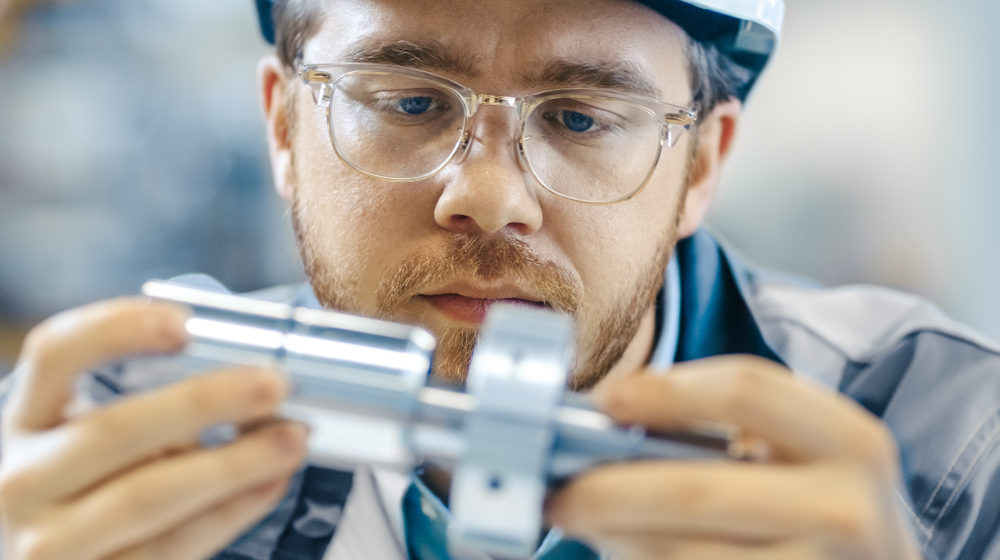
Shifting from OEM-Supplier Design Collaboration to Integration
March 25, 2019
Many original equipment manufacturers (OEMs) design and develop product purely for function – after all, your brand is your product, and it needs to live up to the expectations set by your brand promise.
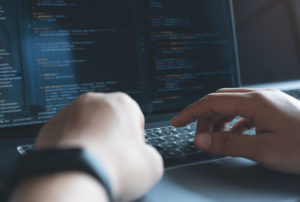
Issues can arise when these functional engineering designs meet the manufacturing floor, however. Perhaps a hole isn’t indicated in the specification that it should be tapped when it should be. Or, perhaps the shifting of a drill hole from one location to another to maximize material usage may translate into significant cost savings. This is when the paths of a typical supplier and OEM often fail to converge to find solutions. But this is also where the relationship of a strategic partner and OEM can flourish – advancing from a simple, collaborative experience to a truly integrated approach.
There are several ways to embark on an integrated design and development process with your strategic supply chain partner. Let’s start with three general, yet effective, areas of focus to better integrate your partners into your OEM value chain of product development:
- Employing advanced technology to improve products and thrive. In the age of digitization, technology can transform the design process. Smartly working with fabrication partners who have adopted advanced technologies helps to create a product development cycle that is more agile, faster, and achieves the desired configuration and quality required for your OEM business to successfully compete globally.
For example, this technology may include the use of artificial intelligence (AI) and machine learning applied to data related to supply, equipment, manufacturing durations, and other data. The horsepower of computing that is inherent in such technology can be a game-changer in developing products faster, cheaper, and better.
In the age of cloud computing, engineering design software allows your design agents to team up with partners to accurately create and develop better designs. Working with partners who are already engaged with such software is key. Thanks to robust integration of data and design using cloud computing and software-as-a-service, designers can consistently use compatible software and platforms to perform different functions and enhance product developments as a virtual team. Technologies by, from, and for all partners are essential ingredients to product development success.
Technology without the necessary human capital would be rendered useless, of course. This brings us to the second area of focus.
- Taking inventory of the human capital found among your strategic partner teams. Capitalizing on the intellect, skills, specific experiences, and more found in the workforce across your strategic partner base helps to positively put the technology to work. Developing a product and moving it from concept to prototype to testing and ultimately to full-scale production requires numerous skills. For example, your fabrication partner’s teams should have strong insight into metals properties and their behavior under different conditions.
Making an inventory of the capabilities and skills found throughout your partners helps access the strengths of one to compensate for the weaknesses of another, or vice versa.
- Building a better supply chain with the strengths and skills of your strategic partners. The third area of focus is finding partner strengths that can aid the manufacturing supply chain for improved product development. The manufacturing supply chain is a complex system of many parts: suppliers, shippers, logistics providers, software vendors, strategic fabricators, and others. All have unique insights and experiences that, when brought together, can contribute to an agile supply chain. Such a supply chain will produce products at a lower cost and a higher standard of quality.
Consequently, knowing your partners’ supply chain strengths and capabilities can greatly assist you in determining other areas of integration, even beyond the product design and development process. In fact, all stakeholders in this value chain stand to benefit from the advancement of a digital fabric that is slowly, but smartly, entering the extended supply chain.
Consultant Bain & Company emphasize the importance of integrating digitization into the supply chain. As they state in their article, “Build a Digital Supply Chain That Is Fit for the Future:” “Companies that integrate digital technologies into their supply chain can quickly improve service levels while cutting costs up to 30%. Just as important are the options that digital technologies provide to develop new business models and new strategies. For instance, leading-edge companies such as Adidas are deploying 3-D printing to move some production closer to customers, offering greater product customization and shorter lead times.”
While the three aforementioned areas of focus can serve as starting guidelines for OEMs seeking to shift beyond collaboration to more of an integrated design and development relationship with partners, the pace of technology and other factors simply mean there are more and more ways in which your OEM business can improve communication, product quality and cost effectiveness.