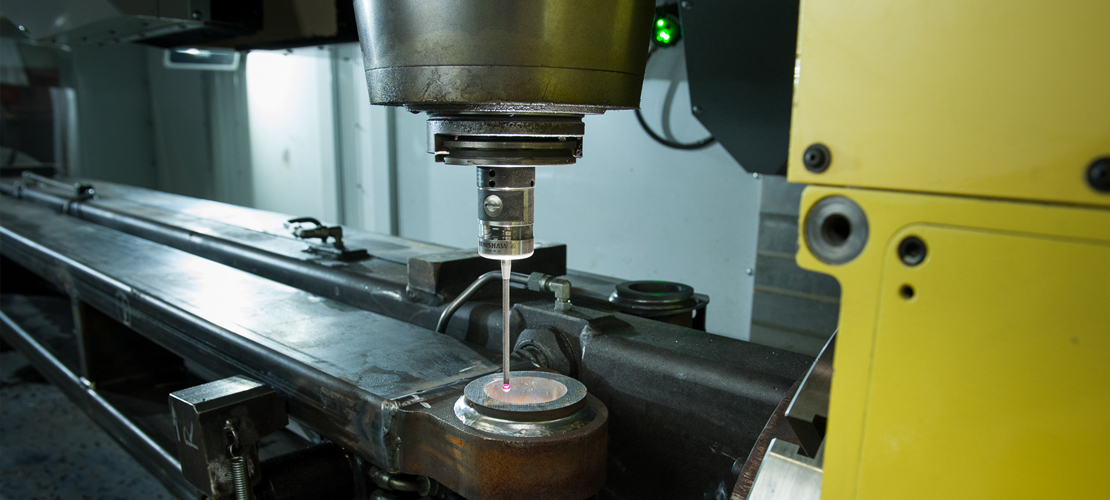
Pursuing Next-Level Improvements to Create OEM Customer Efficiencies
May 15, 2024
Illuminating bottlenecks in the manufacturing process allows companies like Miller Fabrication Solutions to consistently produce the products OEM customers need in the desired time frame. Constraints can’t necessarily be pinpointed, however, simply by observing work.
For 11 years, Miller Fabrication Solutions has been on a mission to continually improve its turnaround time and quality processes by using lean manufacturing principles. More recently, we have begun uniting our lean manufacturing processes with Six Sigma data tools.
Lean manufacturing focuses on efficiency and productivity through waste reduction; Six Sigma focuses on quality through error reduction. Pairing the statistical processes of Six Sigma — controls and data collection — with lean manufacturing drives further improvements in our processes.
Our initial data collection and analysis project stemmed from a capacity concern. Looking 12 months out, based on customer data, we knew we would encounter a capacity constraint on a CNC machine center that has a specific fixture and machines a certain family of parts. We needed to understand the cycle times on the individual parts within that work center so we could generate more capacity on the machine.
Our analysis revealed that more than half of each part’s cycle time was dedicated to probing features for cutting the metal. Of the 27 features being probed, nine presented virtually no risk of being out of tolerance. By eliminating those nine probes, we freed up a few minutes of cycle time on each part. Over the course of a day, those minutes added up and began to generate some of the capacity we needed to meet our customer’s timeline.
After that quick win, we eliminated additional probes by evaluating and modifying upstream processes. These efforts have increased our capacity to produce customers’ products in the required time.
Since that initial project, our expanded Lean Six Sigma work has better aligned projects with our band saws’ capabilities, improved our machine center tooling quality control processes and helped us identify trends and opportunities for quality improvements to ensure our customers dependably receive products that meet their expectations. We now are examining our welding processes to see where we can reduce or eliminate non-value-added work.
We’ve also trained supervisors, crew leaders, mid-level managers, engineers and quality control personnel in Six Sigma quality methodologies, challenging them to identify where they can apply those approaches in their areas. As a result, additional opportunities have emerged for us to realize improvements based on this more strategic and targeted data collection and monitoring.
We are not satisfied with only the low-hanging fruit. Our Lean Six Sigma continuous improvement journey compels us to find the next-level enhancements we still need to reach, and we continue to look harder for the next improvement opportunity.