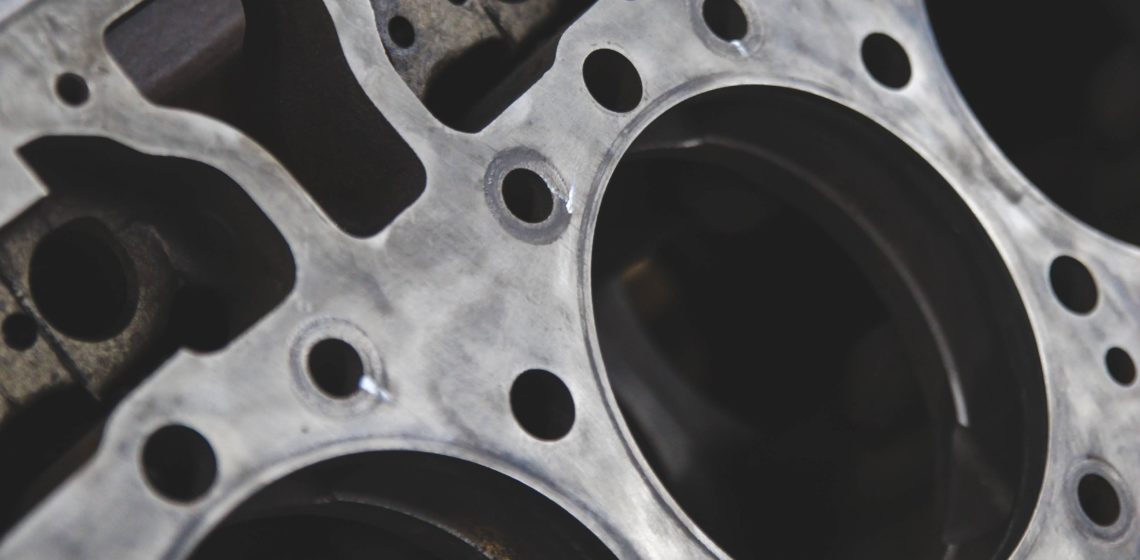
Proven Process Meets Continuous Improvement to Reduce Cycle Time and Enhance Quality
April 4, 2022
Even in today’s challenging manufacturing environment, Miller Fabrication Solutions meets Original Equipment Manufacturer (OEM) demand for complex, prefabricated metal parts, such as engine crankcases and large saddle mount plates. Relying on a proven, end-to-end weldment process coupled with a commitment to continuous weldment improvement, Miller manages supply chain and labor challenges and incorporates value-added solutions that simultaneously lower costs and improve quality.
Recapping the initial stages of fabrication project management
In October, Miller gave customers, prospects and students insights into these vertical integration capabilities during “The Life Cycle of a Weldment,” a two-part webinar series created for Manufacturing Day 2021. Part One of the webinar series demonstrated the first three stages of Miller’s project management process: consultation/quoting, project development and material processing.
- In the consultation/quoting phase, Miller determines project fit, discussing blueprint specifications with the OEM and making recommendations for any modifications that may reduce production costs without sacrificing product quality.
- An internal team of engineering, process development, customer service, planning and quality experts onboard new projects during the project development phase. During this second step in the project management process, Miller customizes a production plan and employs part approval protocols to ensure quality weldments throughout the life cycle of the project.
- In the third, or material processing stage, Miller acquires materials efficiently and cost effectively, transforming them into quality-checked parts that meet every customer requirement. Engineers and highly-skilled trades people use robotics, state-of-the-art machines and proven techniques to cut, grind, weld, machine, blast and paint products to exact specifications, as verified by Miller quality specialists. Each operation undergoes a standardized inspection to review critical checks before a part proceeds to the next stage.
Readying heavy equipment parts for application
In Part 2 of “The Life Cycle of a Weldment” webinar series, Miller highlighted the final two stages of its project management process, where parts are readied to begin their working life.
Stage 4 – Component Completion
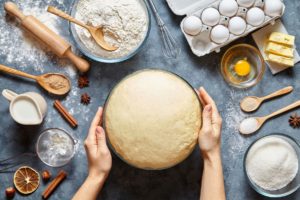
As the name implies, Miller completes projects and handles the kitting process, where separate-but-related items are grouped, packaged and supplied together as a single unit. The kitting shop order, which lists the parts to gather in a kit, is likened to a cake recipe. The “putaways,” or completed components, then are delivered directly to the point-of-use in the manufacturing process. They may be sent to the fabrication shop, which “bakes the cake,” and then the machine shop for “frosting.”
Finally, Miller packages completed components and readies them for shipment to the OEM’s destination location(s), oftentimes a manufacturing plant for finishing touches and full assembly or directly to an OEM’s customer facility.
Stage 5 – Project Review
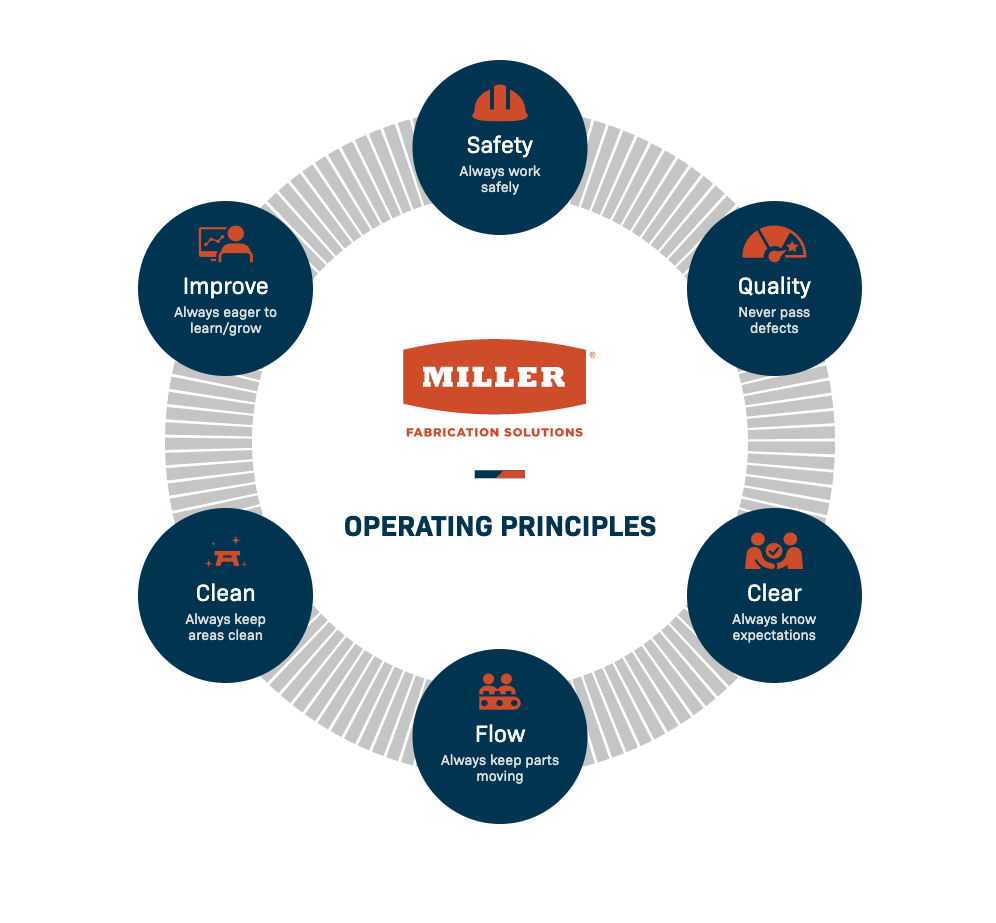
After parts have shipped, a Miller team revisits customer projects to identify opportunities for process improvements. This strategy aligns with one of the fabricator’s six operating principles – “Improve.”
By engaging in continuous improvement, Miller produces better parts faster. Continuous improvement can be in the form of research of new equipment and techniques, including robotics and automation, and applying them to existing processes where appropriate to reduce production setup and cycle time, enhance quality and increase speed and accuracy.
Miller is at the forefront of developing leading-edge processes to produce quality metal parts that consistently meet exacting standards and keep OEM equipment production lines moving. Read more about Miller’s continuous weldment improvement efforts here and contact Miller to learn how your weldment project can be strategically managed for repeatable success.
You Might Be Interested In
August 6, 2021
The Life Cycle of a Weldment, Part 2