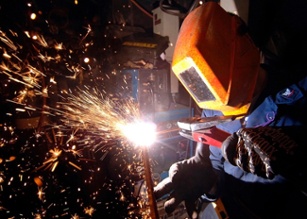
Minimal Defects: 4 Ways A Supplier Improves Your OEM Parts Quality
October 28, 2016
Defective OEM parts impact your production schedule, slowing you down as you send components back and wait for new ones to arrive. That’s why the right contract manufacturer works hard to minimize the number of defective parts you receive.
With higher-quality metal parts, your end product is safer and functions as intended. Customers are likely to associate your brand with quality. You can build on your reputation to attract new and returning customers. Plus, a higher-value product sets you apart from competitors.
While minimal defects sounds like a positive assurance, how does your OEM supplier actually achieve this goal? Your supplier should use the following four techniques to improve the quality of your metal parts:
1. Contains Mistakes To Promote Higher Quality
As much as suppliers work to produce high-quality OEM parts, no one is perfect. Mistakes are bound to happen in any industry, but the key is making sure they don’t reach customers. Suppliers fix problems before they ship components out by containing them.
Metal manufacturing can go wrong in so many places. So, the right supplier implements checkpoints at every stage of manufacturing. Workers inspect parts thoroughly to ensure they meet specifications before sending them along to the next station.
2. Uses Data To Measure And Improve Quality
Your supplier should collect data at each metal manufacturing stage. For example, workers record critical dimensions of each part based on what they recently changed about the part. Directly after industrial welding, your supplier may measure critical welds and ask whether the dimensions hold up to specified values.
A supplier that follows the gold standard in data collection implements the following steps:
- Preserves data
- Uses data
- Shares data results
Not only should your supplier record data, but it should keep data historically and use it to make process improvements that raise the quality of your parts. Plus, you should always have access to supplier data.
You can audit your supplier to ensure it’s using the right processes. Simply ask for data results and see whether your supplier is catching mistakes. It’s a red flag if your supplier isn’t willing to share this critical information with you.
3. Clarifies Your Quality Expectations
Having a process in place is essential to promote high-quality parts. However, your metal manufacturer should also clearly understand your expectations.
When your supplier begins a project, it should send you a test unit and have a conversation along the lines of, “This is what we believe the part should look like. Correct us if we’re wrong.” If a supplier did indeed make a mistake, share that information so it can manufacture your OEM parts to your standards going forward.
4. Sustains Effective Processes
Once your supplier has the correct processes in place, it should continue following them accurately. Suppliers should ask themselves:
- How robust are the processes?
- Can we control the processes?
- What methods do we use to sustain processes?
Employees at your contract manufacturer’s plant move in and out of processes, making sustainability difficult. As people leave and your supplier makes new hires, knowledge must transfer from employee to employee. Your supplier need a process for everything, including educating new workers.
If you know what you’re looking for, you can walk into a supplier’s shop and see whether it focuses on methodologies that promote quality. You should observe workers recording information and keeping work stations organized.
The right supplier is completely open with its operations. Take advantage of that transparency to confirm your supplier is process-driven and doing everything in its power to prevent defective OEM parts from reaching your plant.