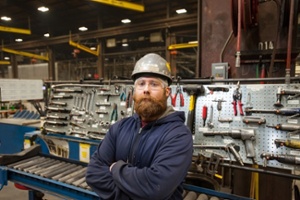
7 Critical Elements An OEM Fabricator Must Have In Place To Promote Safety
September 8, 2017
OEMs usually have very high standards for safety, and they expect the same from their metal manufacturing suppliers. Not only does a safe work culture benefit employees, but it also improves the quality of metal parts your supplier produces.
The right OEM fabricator makes sure safety is its highest priority by putting the following seven program elements into place:
1. Safety Orientation
Your metal manufacturing supplier should give new employees a thorough safety orientation to explain how everyone is responsible for safety, from the newest employee to upper management. This orientation can include the assignment of personal hard hats, ear protection, safety goggles, as well as a safety manual and review of procedures. Safety should be an important part of the onboarding process.
2. Regular Safety Meetings
Regular meetings allow the right OEM fabricator to keep safety on the forefront of everyone’s mind. Not only do official group meetings take place, but supervisors meet with workers individually for a few minutes every week to discuss a particular safety topic. Longer one-on-one meetings can take place throughout the month.
New safety implementations are often added based on employee feedback, making employees a critical source of information and an integral component of safety program improvement.
3. Behavior-Based Safety Approach
Employees may be invested in a safety culture, but if they don’t exhibit safety behavior, they can still get injured on the job.
A contract metal manufacturer should help employees take ownership of their daily activities. The distribution of periodic “wellness bulletins,” for example, are often used to advise employees about healthy ways to alleviate stress, eat nutritiously and get ample rest for the upcoming workday.
Roger Shaw, director of risk management at Miller Fabrication Solutions., encourages workers in a stressed or distracted state to “take a four-second time-out to gather your mental attitude.” This short time span can mean the difference between making a devastating mistake and avoiding issues altogether.
4. Employee Knowledge Of Safety Policies
All safety policies should be easily accessible to employees. Your metal manufacturer should have a comprehensive safety library available with policies detailed in both electronic and hard-copy form.
In alignment with a behavior-based safety approach, however, ideal contract metal manufacturers should promote peer safety discussions outside of formalized safety meetings. These safety discussions may be tracked by department and contribute to an overall rating that fosters employee initiative.
5. Open Communication Regarding Safety Incidents
Visibility into safety policies and recent incidents is vital to the safety culture of a leading contract metal manufacturer. It strengthens employee relationships, safety programs and the overall quality standards of finished goods. Safety newsletters or similar updates are often distributed on a monthly basis to keep employees informed about safety related news, with open lines of communication between safety management, supervisors and employees to ensure all questions, comments and observations are addressed.
6. Dedicated Safety Committee
Forward-thinking contract metal manufacturers have safety committees in place to review safety incidents and put containment measures in place as a result of those assessments.
The committee is also responsible for:
- Setting goals as to how often supervisors meet with employees to discuss safety
- Developing new ways to raise employee awareness of their contribution value
- Empowering managers to implement safety solutions based on employee feedback
7. Routine Safety Inspections
Supervisors at your metal manufacturing supplier often conduct their own inspections within their department on a daily basis. Usually, a supervisor will inspect based on a certain subject, such as:
- Personal protective gear – Is everyone wearing the gear?
- Lifting devices – Are the devices in good working order?
- Guards on hand tools – Are the guards in place?
- Housekeeping – Are the work centers clean and free of hazards?
How A Metal Manufacturing Supplier’s Safety Benefits OEMs
Having a safe work culture benefits a metal manufacturer’s customers by positively impacting the quality of the product a supplier produces. Put simply, the safer the environment, the greater the employee focus on product details – from design spec reviews and production to inspection and delivery.
Whether it’s keeping workstations organized, focusing on the task at hand or using guards on hand tools, the smooth execution of safety procedures makes it easier to produce high-quality work the first time and prevent re-work.
The right OEM fabricator promotes a safe work culture to protect its employees, match your priorities and keep your production lines running with a steady stream of high-quality parts. If safety is important to you, make sure your OEM fabricator feels the same way.
You Might Be Interested In
Corporate
March 12, 2025
Pam Elkin: A “Miller Lifer”Corporate
December 16, 2024
Investing in Our People: Miller Reinstates Weld School