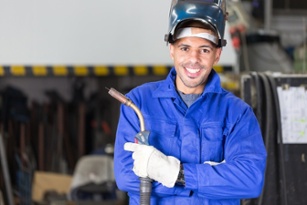
4 Assets Of A Contract Supplier That Has Your Processes Under Control
December 30, 2016
While you may feel pressure to control your metal manufacturing processes at all production stages, everyone needs a break to re-focus their energy at times. Taking a step back is difficult when so much is at stake. Will your parts arrive on time and in pristine condition? You have to trust your contract supplier to manage your metal parts production reliably.
To keep your metal manufacturing processes under control, your supplier should use the following four major assets to its advantage:
1. Equipment Flexibility
Manufacturing equipment shouldn’t be static. Your supplier must carefully consider its equipment layout for each project. The right contract supplier uses tools like spreadsheets, calculators and models to evaluate production flow and move equipment as necessary.
By keeping related equipment together, your supplier limits material handling. This also reduces the risk of damaged and lost parts, impacting your product quality and on-time delivery.
2. Optimization Data
Analyzing data is essential for planning a project’s production line. Calculations like run time and takt time tell suppliers how long they have to complete each operation based on customer demand.
Take time measures the time between the start of one unit’s production and the next. If a supplier can’t hit its required takt time, it won’t be able to meet your demand. However, a strategic supplier knows how to optimize its processes so you receive your parts on time. If a metal part takes three hours to complete but production requires one every hour, your supplier should add three of the same machine to the line so production flows steadily.
3. Process Controls
Once your OEM supplier optimizes its processes using available data, it must control them. That means staying within the budgeted time frame and not letting pieces move downstream damaged. Both of these factors impact your bottom line from an efficiency and quality standpoint. Your supplier may need to make tweaks and adjustments to stay on track.
As anyone who has ever cleaned up a cluttered garage knows, sustaining change is difficult. You may spend a weekend organizing items in your garage and resolve to keep it clean. However, you must carefully maintain a pattern of organization to prevent clutter from coming back, and the same principle is true of sustaining metal manufacturing processes.
4. Lean Manufacturing Experts
Your supplier should have experts trained in lean manufacturing on the floor supervising processes and sustaining efficiency all day. These experts look for and minimize waste in the following seven areas:
1. Overproduction
2. Overprocessing
3. Waiting
4. Transport
5. Inventory
6. Motion
7. Defects
Metal manufacturers should categorize waste into avoidable and unavoidable waste. Suppliers may not be able to control some waste. For example, if your supplier has a 1,000-pound plate and cuts it into 10 pieces that are 80 pounds each, 200 pounds of scrap are left over. This scrap is often unavoidable, perhaps because you need circles or un-nested shapes cut out of the plates. The shapes may simply create space between one another when laid out on a plate.
On the other hand, suppliers can sometimes reduce scrap caused by steel-cutting methods that use heat, which burns a portion of material to dust and distorts the steel between pieces. Your contract supplier may decide to use a water jet to cut steel so it cuts pieces that are closer together. A supplier’s job is to make its methods as productive as possible. Focusing on reducing avoidable scrap helps you save on material costs.
When your manufacturing supplier uses these four assets to control your production processes, you don’t have to worry as much about supervision. And, when you’re confident your manufacturing needs are covered, you have more time to focus on other strategic areas of your business.