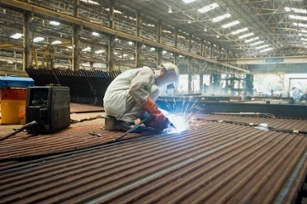
3 Ways A Welding Expert Ensures Your Production Line Keeps Running
January 6, 2017
With a precisely executed production schedule, you’re able to fill your customers’ orders on demand. Avoiding problems like defective metal parts and late supplier shipments helps you minimize production downtime. But component quality should be a given if you’re working with the right contract supplier.
Not only do you need the basics covered, but you also need a welding expert that understands the finer details about how to keep your production line running. From data expertise and inventory management to strategic collaboration, your welding contractor should support your OEM production in the following three ways:
1. Practice Insightful Data Management
Your welding contractor should ask for your forecasting and demand data and interpret it skillfully.
Sometimes, that means looking beyond the raw data and examining how many machines you plan to build in a certain month. For instance, if you’re manufacturing six asphalt rolling machines in August and your welding contractor is supplying the frame, it knows to build six frames in July.
Raw data is intensely complex and easy to misinterpret. Your supplier should always consider it within the context of your production schedule. Using a model structure in planning provides a higher-level overview of what parts you’ll need and when.
2. Plan For Demand With Smart Inventory
A welding expert uses a formal process to manage your demand and prevent production downtime at your plant. It should have a department dedicated to analyzing data, interpreting algorithms and making informed decisions about what level of inventory is right for your business.
Being too lean is an important mistake to avoid in inventory planning. Too little inventory negatively impacts both you and your supplier’s operations. Your supplier should offer smart inventory, finding the right balance when it comes to stock levels.
If you run into a problem or need to ramp up quickly, your supplier’s inventory position must deliver accordingly.
As a customer, you should be aware of what your supplier plans to produce as a stock item or non-stock item. Behind-the-scenes planning drives good inventory decisions.
3. Challenge You To Provide Accurate Data
You are responsible for giving your supplier accurate plans based on your expected demand. A welding expert understands these are just forecasts, but data that is completely off base may slow down your production.
Your supplier must challenge you to provide accurate data. That way, it doesn’t build too many of the wrong components (perhaps for a model you’re phasing out) and keeps the right metal parts in stock for emergencies. Since your supplier is providing you a service, you should mutually agree that any extra inventory will eventually be used.
If you want to keep your production line running smoothly, consider sitting down with your supplier and reviewing its strategies. Is data driving its inventory decisions? You should also be comfortable with the stock levels it maintains.
Your supplier will deliver a floor schedule to its internal team that is feasible within a given time frame and supports your forecasted demand. As a result, you receive the parts you need on schedule and minimize production downtime.