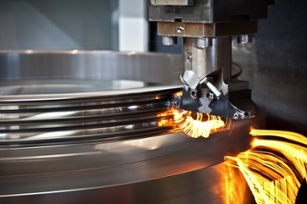
Is Your Metal Fabrication Supplier Addressing Inefficiency?
July 27, 2016
Some metal fabrication suppliers fail to address inefficiencies, deprioritizing your cost savings, quality and on-time delivery. Perhaps the supplier lacks the infrastructure to implement change, or maybe it’s just not a process-oriented company.
In many cases, OEM suppliers adopt an attitude that metal manufacturing services have “always been done this way.” Such a mindset only encourages your supplier to stagnate, which prevents it from keeping up with your demand increases as you grow.
Common Inefficiencies Suppliers Fail To Address
You may already have read about some of the inefficiencies involved in designing parts for machining that cost you extra money. For example, unnecessary text, thick walls, deep holes and small features are time-consuming to machine and expensive.
Material waste is another inefficiency that detracts from your budget. For example, you should try to design parts that are easily nested. Your metal fabrication supplier will bill you for all material, even the waste.
You should also standardize materials to help reduce waste. Try to use as much market-available material as possible, and design for common sizes and grades. Special mill orders take extra time, adding to your costs.
Techniques To Improve Manufacturing Efficiency
To improve manufacturing efficiency, your supplier should optimize processes with multiple operations that move across several machines. However, your supplier must ensure that it improves overall efficiency, not just the efficiency of individual processes.
It’s possible to reduce the time it takes for individual metal fabrication, industrial welding, machining, finishing and assembly services yet add time in other areas. One employee could move twice as fast during a certain process and congest the employee working on the next stage, slowing him down.
Your OEM supplier must look at the entire cycle and identify opportunities to improve. Expertise and experience are necessary to increase manufacturing efficiency across all processes.
One impactful technique to improve efficiency is time analysis. A supplier uses either a stopwatch or time clocks connected to a computer to uncover processes that result in a net loss. When performed well, it gives your supplier a complete picture of its operations. Time analysis sheds light on inefficiencies in areas such as:
- Plant layout
- Material flow
- Management practices
- Shop functions
- Purchasing activities
Packaging can also be optimized to increase efficiency. Your supplier should be an expert on shipping container design so it can pack more metal parts and assemblies in a single shipment. You save money when a supplier helps you reduce trips back and forth to your facility.
A supplier that maximizes its manufacturing efficiency helps you cut costs, but it also benefits you in other ways. When your demand shifts, an efficient supplier can accommodate you. You have a reliable source for parts and assemblies to keep your own production lines running. With the right supplier, you’re able to focus attention on your operations and make improvements that revitalize your business.
Interested in partnering with Miller? Contact us today.