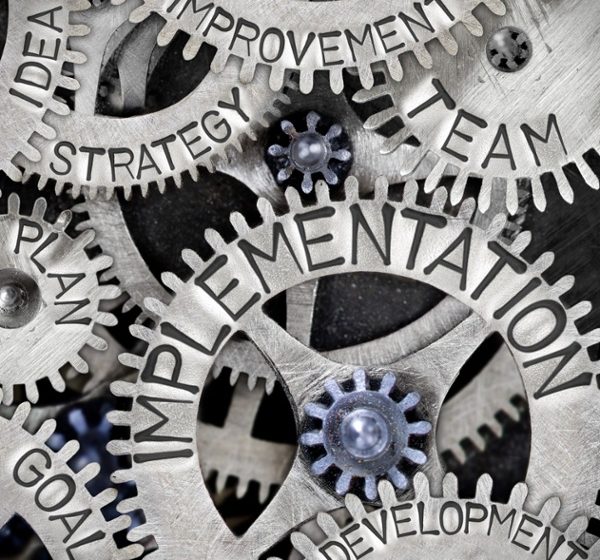
When a Partner’s Process Improvement Efforts Fall Short
June 5, 2018
When it comes to process improvement, there is no shortage of methodologies. However, one thing that is rarely discussed is what to do when those efforts fall short – even though you’ve probably seen this happen quite a few times in the past, as most improvement efforts can fail to meet their targets.
If the problem is internal, it can be “relatively easy” to deal with as additional resources can be provided. The situation gets complicated when your fabrication partner’s process improvement efforts fall short. This can be a challenge for supply chain managers, as you not only need to ensure delivery schedules remain intact, but also need to work through your partner’s team to get efforts back on track.
The Importance of Process Improvement
For decades companies have undertaken process improvement initiatives to increase efficiency, improve quality, and reduce costs. While these initiatives have transformed manufacturing, they are complex projects requiring the support of the entire organization.
Given the complexity, why would any organization want to undertake something so fraught with danger? The answer usually comes down to at least one of four factors: Customers, Competition, Cost, and Technology.
When you think about it, the voice of the customer has a lot of pull in supply chains; it doesn’t matter if it is a strategic metal fabrication partner or a tier-3 parts supplier – if the customer wants something, it gets done. Therefore, customer requests can weigh heavily in the decision to undertake a process improvement project.
But the reason to undertake a change project doesn’t always depend on customers, as competitive forces can also play a role – particularly if a partner is losing out on competitive bids or needs to compete with low-cost providers halfway around the world.
Sometimes the need to reduce cost isn’t necessarily driven by competitors, rather it is the need to improve profitability. Or it could be the introduction of new technologies that can have a transformative impact on supply chain operations.
Either way, process improvement projects have become an important part of manufacturing today. As such, undertaking a change management initiative tends to yield outsized returns for all those involved.
When Things Go Wrong
While the reasons for undertaking an improvement project are important, one point that is often lost is the complexity inherent in a change, which often involves multiple organizations – both upstream and downstream.
This complexity stems from the risk of missing the mark on integrating improvements across the supply chain. When this happens, the changes are nothing more than “Point Kaizen” and could end up degrading the entire process.
Adding to these challenges is the fact that globalization has extended most supply chains. This makes it harder to work seamlessly on complex matters, such as visibility.
These factors raise the stakes for process improvement projects and can have a big impact when things go wrong. The question for supply chain managers becomes: to what extent will you need to get involved with a supply chain partner to correct the situation?
The answer often depends on the following:
- What is the immediate impact on the supply chain?
- Is a second source available and can it be ramped up quickly?
- What will it take to help the partner meet their goals?
The answer will also be determined by the supplier-partner strategy. For example, some organizations place value on working with supplier-partners to build capabilities, while others expect the partners to provide this expertise on their own.
In addition, one concept which has begun to take hold in supply chain management circles is the Functional Supplier Quality Process Framework (FSQP). While some managers believe this approach is tantamount to taking over a partner’s quality and improvement processes, others see it as an opportunity to increase collaboration.
Beyond this, supply chain managers should review how a partner elevates the issue internally. For example, do they shrug off the setback or do they act by increasing direct oversight from senior management as well as adding resources – both internally and externally? This sort of rapid reaction can make all the difference in the world, and it might be enough to get the process improvement initiative back on track.
As you can see, process improvement plays a key role in modern manufacturing. While many projects miss their intended target, this doesn’t mean that supply chain managers are powerless in the process.
Instead, supply chain managers should keep a close eye on their partner’s progress, using this as an opportunity to increase collaboration. By doing so, you can increase your understanding of your partner’s capabilities as well as shield supply lines from unexpected disruptions due to a delayed process improvement project.
You Might Be Interested In
Blog
January 27, 2023
Consolidating Suppliers Reduces OEM Supply Chain RiskQuality
February 2, 2021
Process Improvement is the Key to Winning