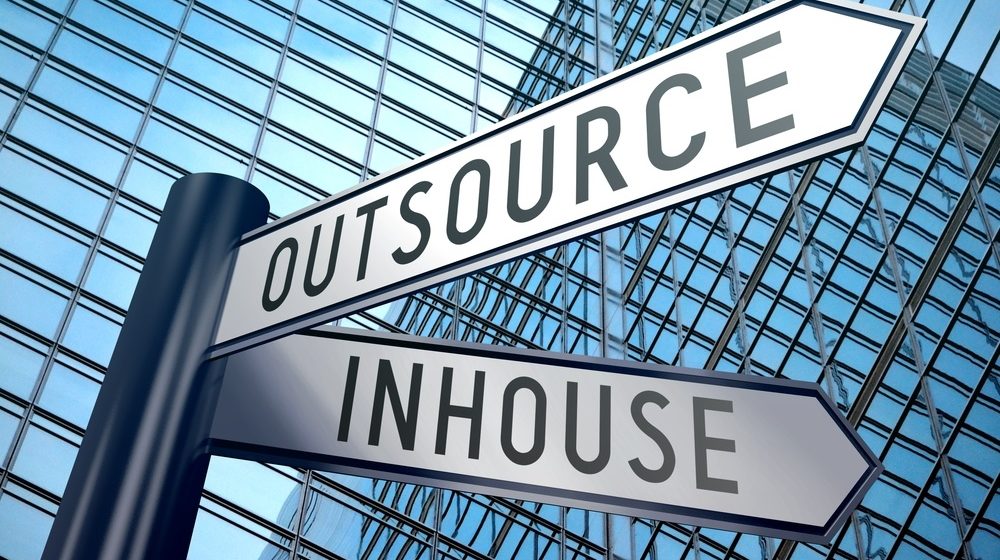
Pros and Cons of Outsourcing OEM Parts fabrication
July 12, 2018
Outsourcing: it is why supply chain management is both an art and science. On the one hand, there is the need to keep proprietary processes and design secrets in-house, while the realities of the market make it impossible for OEMs to produce everything themselves.
Metal parts fabrication is where this dynamic often comes to the fore, as OEMs balance the goal of complete vertical integration with constraints, such as finances, time, and know-how. In response to this, many choose to outsource the production of a part or an entire assembly.
While some executives view outsourcing as an opportunity to reduce costs, most manufacturing engineers understand that it is not always that simple. Hidden costs can easily undermine the basis by which most ‘make or buy’ decisions are made.
As such, this post is intended to guide you on the pros and cons of outsourcing OEM parts fabrication. This primer will give you some of the insights needed to gain a deeper understanding of the impact of an outsourcing decision, and more importantly, how to make it work for your company and your customers.
Vertical Integration is a Myth
That’s right, the idea that any OEM can keep most of its supply chain in-house doesn’t quite add up. For starters, you need to get your raw materials from somewhere and owning mines and smelters costs a lot of money. Beyond that, there is a time when outsourcing the manufacturing of a complex part or assembly makes more sense than doing it in-house.
Reasons include the capital costs connected to purchasing specialized equipment to line-balancing issues tied to bringing an important, yet non-mission critical, process in-house. This includes the perception that controlling the production of highly-specialized products would give OEMs an advantage over their competitors.
Another reason for pursuing vertical integration is the ability to control margins – especially as the OEM wouldn’t have to pay markups. Then there is the argument for reduced transaction costs, tighter control of labor costs, and improved quality.
However, it doesn’t always work out this way and, by and large, vertical integration is much easier to talk about than it is to achieve.
The Case for Outsourcing
If vertical integration is a myth, then most OEMs must be outsourcing 100% of their manufacturing processes, right? Well, not exactly. Yes, outsourcing is the opposite of complete vertical integration but in the real world, the two represent the extremes of a continuum.
As a supply chain professional, you have probably seen this play out in real time. In some cases, there is a strong argument to be made for keeping a process in-house, while in other instances an OEM might decide the case for outsourcing is more compelling.
But how are these decisions made? Hopefully with data, such as a detailed analysis of existing supply chains and potential alternatives. This includes looking at the entire system cost, including the risks.
For example, a metal fabrication partner in the U.S. might not be able to deliver the ‘China Price’ but in some instances, the risks related to having a supply chain that stretches halfway around the world outweigh the benefits.
As such, there are some questions to ask when making the case for outsourcing:
- Will the move to outsource manufacturing processes free up assets?
- What world-class technologies or efficiencies does the supplier partner offer that aren’t available in-house?
- Does the decision to outsource move production closer to customers?
By asking these questions, you will gain a deeper understanding of how the decision to outsource a process, or not, will impact your organization.
The Pros and the Cons
As mentioned, full vertical integration and complete outsourcing represent the extremes of a continuum. Furthermore, there are some questions you want to ask when considering outsourcing a process.
What are the pros and the cons of outsourcing parts fabrication?
Pros |
Cons |
Non-core processes handed over to manufacturing experts | Need to establish supplier partner management framework – this includes due diligence, compliance, and quality assurance |
Increased Return on Capital Employed (ROCE) by shifting capital requirements off the organization’s balance sheet | Risk factors including supplier partner risk, reputational risk, and IP risk – this points to the need for a strong supplier partner management framework |
Access to world-class technologies and processes | Impact on scheduling, as deliveries need to be aligned with in-house production |
Improved line balancing | Impact on inventory, as buffer levels might need to be increased |
Opportunity to move production closer to customers |
In the end, the best decisions are based on data, as each situation is different. Just keep these pros and cons in mind the next time you are considering outsourcing your OEM parts fabrication.