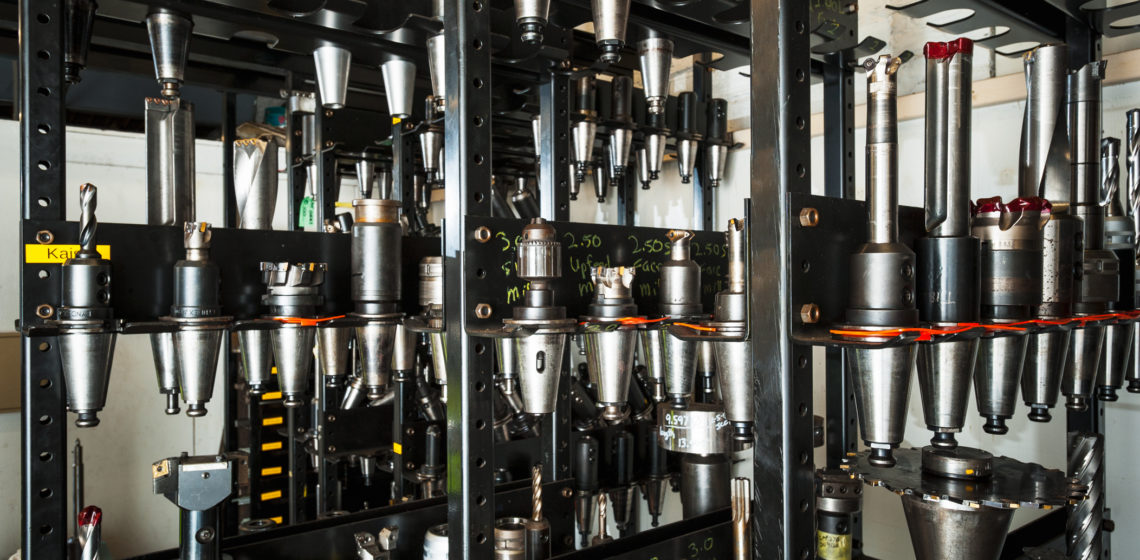
3 Ways to Minimize Metal Fabrication Costs
May 4, 2020
With drastic drops in market demand due to the COVID-19 pandemic, manufacturers across agriculture, construction, mining, oil & gas and other industries are looking for new and creative ways to reduce costs and improve margins. For procurement professionals, this means engaging supplier-partners in cost reduction programs and other initiatives to maintain or exceed product quality while minimizing fabrication costs. Industry veterans know that it quickly becomes an exercise in finding the small tweaks that can add up to big savings.
To that end, here are three methods you might be able to use to reduce your metal fabrication costs.
Consolidate Services
Engineering design, raw material sourcing, assembly, logistics and other processes can be performed by different companies and services, depending upon the equipment manufacturer’s supply chain, their industry and other factors. It’s worth looking at these processes holistically, however, and researching what savings could be achieved by consolidating the management of those services in one company. Supplier consolidation can be a great way to streamline processes while keeping other incidental costs down, as there’s only one company to communicate with instead of five or more.
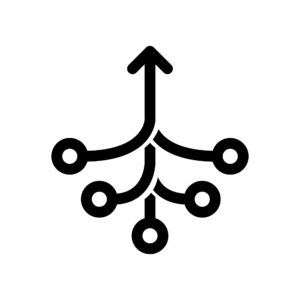
For Tier 1 fabricators who purchase raw materials for a number of equipment manufacturing customers, there is a developed purchasing channel that is experienced in following market trends and sourcing the right materials, at the right time, at the right cost, in the right quantities. Similarly, these metal fab supplier-partners would have a logistics arm to support packaging and shipping requirements through its own fleet or work with the preferred carrier of the Original Equipment Manufacturer (OEM) itself. It’s vital that the metal fabricator is vetted and audited correctly, of course, in order to head off communication, quality and other issues as early in the relationship as possible. But consolidating your processes in the right organization can dramatically reduce plate fabrication costs.
Design for Effectiveness and Efficiency
Just as product must be designed to deliver end-user efficiency, so to must it be designed for production efficiency. There are a few common areas in which an engineering-design partnership with your Tier 1 supplier-partner can net these kinds of efficiencies, as well as other benefits:
- Tight tolerances. Any project will have exact specifications that need to be met, and certain tolerances that can’t be exceeded. Metalwork requires tight measurements, and it will be critical that project designs account for those accordingly. At the same time, if tolerances are unnecessarily tight, you could make the project more difficult – and longer and more expensive – than it needs to be.
- Flexibility. Use common gauges of metal. If possible, design parts that can be used in more than one way or more than one machine – although that isn’t always possible. As mentioned above, keep your tolerances as high as they need to be, but not so high that you routinely disqualify otherwise acceptable parts.
- Simplification. This last element requires a skilled designer and fabricator that knows how to keep metal folds simple and lines clean. When producing a final design for fabrication, just remember that all else being equal, simpler parts are easier and, therefore, more efficient to produce.
Reduce Waste
Reducing waste is more of a long-term goal than an immediately-achievable end. Sometimes a simple manipulation to a design may yield more parts from a single piece of raw material, or you might hit on a way to reuse the scrap from one project to produce another one. These are quick-and-easy ways to look for waste reduction. But in many other cases, reducing the amount of waste may require predictive maintenance on machinery and retooling entire manufacturing processes.
While expensive and time-consuming, waste reduction goals are worth pursuing because they tend to produce long-term savings. One extra part per piece of raw material may not seem like much if you get 1,000 parts out of it; but if you’re producing hundreds of thousands of parts per year, over the lifetime of your process, those savings will add up.
Get Creative
While service consolidation, waste reduction and design efficiency are some of the ways OEMs can look to minimize steel fabrication costs, there are a number of creative options out there to explore with your Tier 1 metal fabricator. Strategic partnerships with such suppliers lend themselves to an open and collaborative relationship that can not only help you achieve your immediate goals, but set the stage for future joint successes. Discuss the supply chain goals of your equipment manufacturing company with Miller by scheduling a consultation with one of our sales account representatives today.
— Authored by guest contributor, Bailey Hudson, a freelance industrial writer who focuses on quality industrial equipment and modern manufacturing. Bailey is currently a staff writer for The Long Reach, covering emerging industrial news.