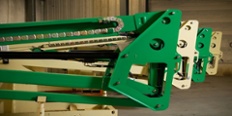
What Coating And Finishing Technologies Are Right For Your Metal Parts?
March 16, 2018
No matter which coating technology you choose, preparation is the key to quality metal coating. To ensure a flawless finish, your fabrication partner must thoroughly clean each part using advanced pretreatment methods.
Powder coating and liquid coating are the two most common finishing processes for OEM parts, and a strategic fabrication partner can help you make the best choice.
Read on to learn how to decide which metal coating process is right for your parts.
Prep Work
Prep work will factor into your metal coating costs. It’s often tempting to cut time on prep work to save money, but the material needs to be cleared and blasted, and dust must be cleaned prior to finishing. Otherwise, imperfections may affect the paint profile.
Preparation accounts for about 80% of the finishing process, according to Steve McPherson, project administrator at Miller Welding & Machine Company. After being blasted on an automatic line, metal parts undergo a chemical conversion so that the paint product will stick.
Powder Coating
The powder coating process takes place when additives, pigments and resins in a powder form are electrostatically charged and applied via compressed air. In comparison to liquid or “wet” coatings, powder coatings offer better protection against chipping, scratching, UV rays and corrosive elements.
Powder-coated components don’t require overly protective handling after cooling from curing. As an article from The Fabricator explains, cured parts can be sent right away to downstream processes, such as assembly or packaging. This can make the fabrication of your metal parts more efficient, saving you money and enabling quicker deliveries.
Powder coating is a durable option suited for outdoor applications, such as agricultural and construction equipment. When working with fabrication partners with existing powder coating capabilities for oversized metal parts, the long-term costs of applying powder can be lower compared to liquid coating applications.
Liquid Coating
Liquid coating is often used to finish parts featuring delicate materials, such as a metal cylinder with a rubber seal, because high temperatures aren’t necessary for drying.
One of the advantages of liquid coating is that it allows you to build a thicker coat. Conversely, your strategic fabrication partner may also be able to achieve a very thin coating (coat thickness can be as low as 0.5 mil). Some liquid coatings can be achieved in one coat, but in other cases you may need three to four coats for a desired finish.
Time And Cost Efficiencies
A powder coating is cured in an oven. The process is efficient, usually requiring about 30 to 45 minutes in the oven. Powder coating requires less prep time than liquid coating.
With liquid coating, materials don’t need to go in an oven, but they can take days to dry otherwise. Using oven heat, liquid coating takes several hours to cure. Often, the price of liquid material can be up to four times higher than powder coating material. Due to time and costs, powder coating tends to be less expensive overall.
Metal Fabrication Partner Capabilities
For complex, labor-intensive part manufacturing, choose a metal fabricator with automatic lines that can handle exceptionally large heavy equipment parts. Also, look for a partner with the ability to manually coat parts, if there may be a need.
Your partner should be technology-driven and use a barcode reader to identify where parts are located in the manufacturing process, in order to ensure parts are moving along efficiently.
Couple the right metal coating technology for your components with the right strategic fabrication partner, and you’re well on your way to extending the lifespan of your equipment and improving its appearance.