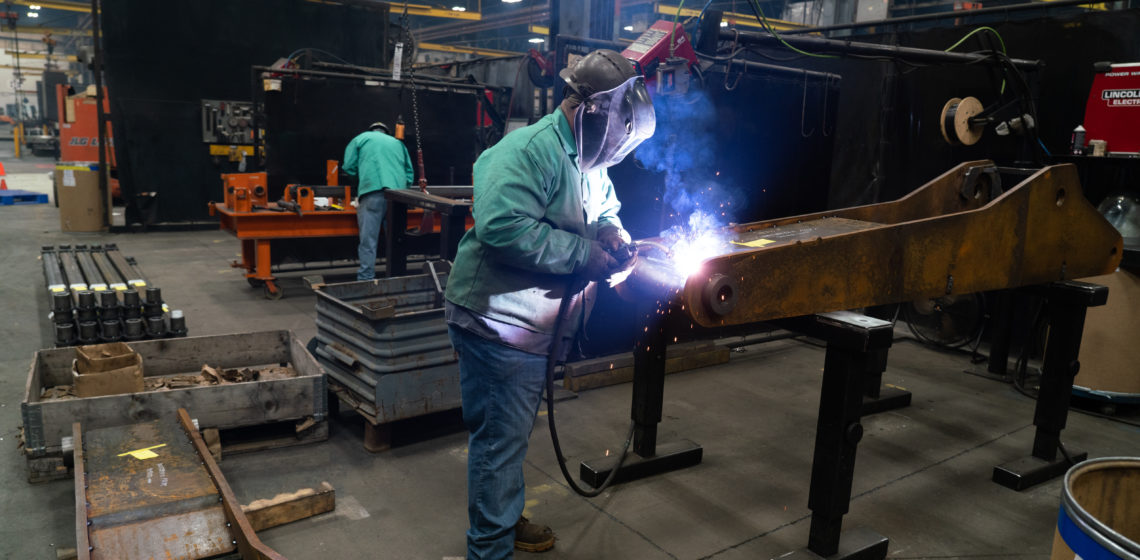
Single-Source Weldment Project Management Ensures Quality, Reduces OEM Risks
January 10, 2022
By managing the fabrication process of a weldment end-to-end, Miller Fabrication Solutions mitigates risks to Original Equipment Manufacturers (OEMs) – including supply and labor shortages – to ensure the on-time delivery of high-quality products, such as chassis, screed frames, engine mounts and other complex parts and assemblies.
This type of production is a core competency of Miller, as a strategic supplier-partner to OEMs. Parts are fabricated from metals like carbon; alloy and stainless steels; high-strength, low-alloy metals; and red metals like copper, brass and bronze, up to two inches thick and processed up to 10 inches in plate thickness.
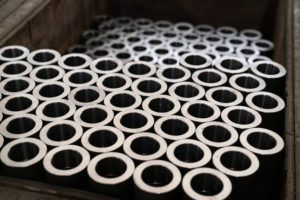
Far more vertically integrated than a typical job shop, Miller provides start-to-finish capabilities – from design collaboration, forming and machining to welding, painting and assembly – as well as value-added services that result in greater quality, lower costs and a streamlined OEM-supplier relationship.
The resulting weldments are frequently used in applications necessitating a high degree of worker safety, such as material handling, transportation and construction equipment; therefore, Miller employs strategic methods to manage each project in order to carefully capture and execute upon every detail to meet or exceed customer expectations.
Weldment project management strategy
Miller gave the general public a behind-the-scenes look at its project management processes through a two-part webinar series, “The Life Cycle of a Weldment” as part of its involvement in Manufacturing Day 2021. In its first webinar, Miller team members described the initial three stages of the company’s project management function and how these stages prepare product for full production runs.
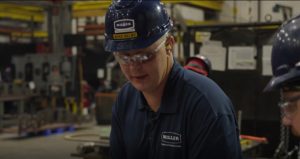
Because every customer project is distinct, Miller takes a flexible and collaborative approach, working closely with customers to understand the design and production requirements while adapting its processes and plans to match those specifications. Definitive solutions like Value Analysis/Value Engineering (VA/VE) and Capacity Management are enabled to help reduce costs, ensure adherence to timelines and improve overall product manufacturability. Through a combination of value-added solutions, a heavy focus on process development, optimization and continuous improvement, Miller readies itself to onboard new work, particularly innovative and challenging parts, to keep production lines moving for industry-leading heavy equipment manufacturers.
This project management methodology takes the “heavy lifting” off global OEMs by reducing the resources required of them to ensure project success and giving them the peace of mind that comes from partnering with a true supplier-partner. It’s part of the reason why OEMs select and depend on Miller as a strategic supplier for some of their more challenging metal part and assembly designs.
The initial stages of fabrication project management
The first three stages of Miller’s project management process include:
Stage 1 – Consultation/Quoting
While Miller handles projects of many sizes, the company primarily manages heavy weldment fabrication projects of $1 million or more annually to establish and maintain long-term, strategic relationships. During this initial stage, project fit is determined by project types, materials involved, specifications, tolerances, timelines and other criteria. This stage is often a dynamic interchange between Miller and the OEM, in which modifications may be recommended, tolerances may be further defined or tweaked and timelines and Estimated Annual Usage (EAU) are verified.
Stage 2 – Project Development
During the project development phase, which begins after customer approval of a project proposal and quote, Miller reviews and confirms customer requirements with internal teams, finalizes required or previously agreed-upon modifications and customizes a project plan.
Miller engineering and process development experts convene during a kickoff meeting to determine how to most effectively move the project throughout processes and determine appropriate fixturing, machinery, tooling and other necessary configurations. Representatives from customer service, planning and quality departments also participate in this meeting. Some of their related responsibilities include:
- Designing capacity/scheduling plans to accommodate required lead times;
- Crafting QA/QC processes to minimize potential errors; and
- Reviewing any customer-requested changes, verifying adjustments and communicating with customers.
Miller’s production part approval process (PPAP), or First Article process, which includes product evaluation from component level to finished part, begins during this stage. Dimensions are checked at component level to ensure a replicable build of the top level. The top level dimensions are then verified to ensure accuracy before a weldment progresses through the manufacturing cycle, securing a repeatable, reliable process that assures customers of a quality product with each Miller shipment.
During this stage, OEMs can realize the benefits of Miller’s value-added solutions, such as identifiable cost savings and speedier output based on Miller’s lean systems and automation technologies.
Stage 3 – Material Processing
This stage comprises:
- Material purchasing, cutting, grinding;
- Part welding, machining, blasting and painting; and
- Quality operations.
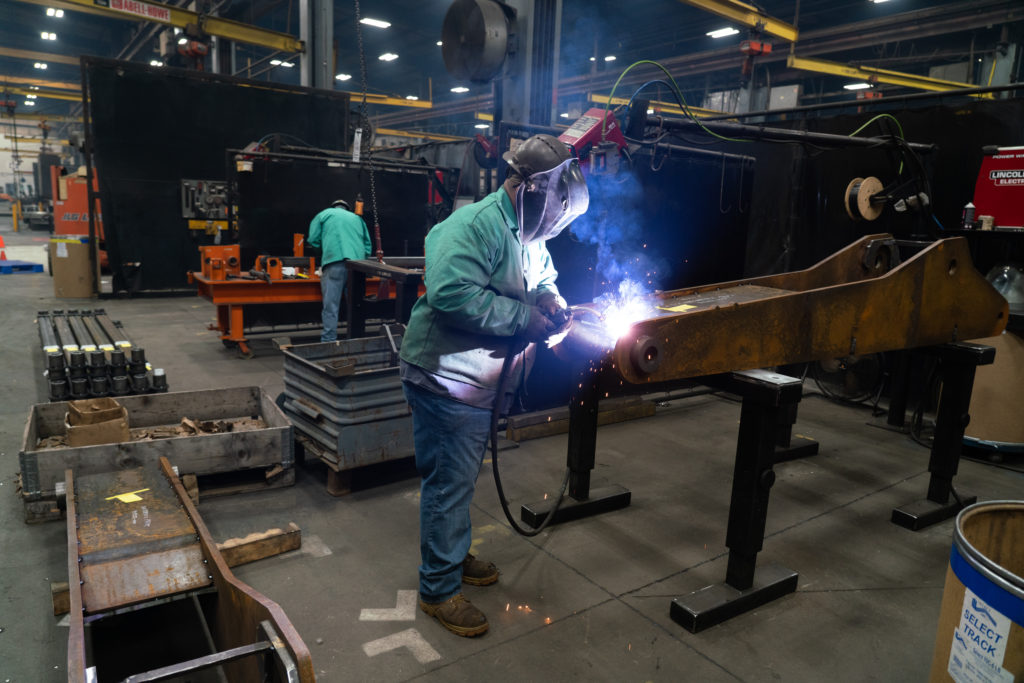
Miller capably handles the complexities of material purchasing and processing from beginning to end. Raw material may be secured in several ways, depending on OEM preferences, cost and availability. For example, Miller may work with an OEM’s sanctioned provider, leverage existing relationships with alternate suppliers or employ a combination of both methods to decrease supply chain issues and meet customer budgets and lead times.
The breadth of Miller’s in-house processing capabilities differentiates the top OEM fabricator from other supplier-partners, as the steel fabricator can take on a variety of value-added work while also joining forces with OEM supply chain networks in support of established relationships and expertise. Miller Fabrication Solutions essentially serves as a single point of contact to provide a seamless experience, handling every aspect of complex weldment projects.
Stay tuned for the last two stages of Miller’s project management process in the next part of this blog series.
You Might Be Interested In
Construction
February 23, 2018
Constructing Your Smart Supply Chain Network