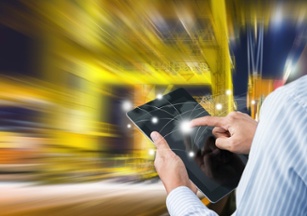
How To Improve Your OEM Supply Chain With Inventory Management
August 19, 2016
Managing your customer and supplier relationships are important supply chain components, and experts say inventory management is the foundation upon which these relationships are built.
Your production lines take a hit if a metal manufacturing partner fails to deliver parts when you need them. At the same time, holding excess stock is costly. Managing inventory helps you balance demand and supply. You account for both upstream supplier purchases and downstream customer needs.
Inventory management is a shared responsibility between you and your supplier. If your OEM supply chain is not completely healthy, it may be time to analyze specific metrics and take a closer look at your supplier’s inventory movement and storage.
Assess Your OEM Supply Chain Health
Your manufacturing supply chain is vulnerable in areas that aren’t always immediately apparent. Many factors that influence your OEM supply chain are inventory related. Keeping a close eye on these variables is critical. To assess the health of your parts inventory management, you should routinely analyze the following metrics:
- Inventory levels
- Capacity utilization
- Materials lead time
- Forecast accuracy
- Inventory days of supply
- Inventory aging
- Asset turns
Set benchmarks to measure your success as you look into these metrics. If they’re available, use industry standards to judge your OEM supply chain health in each area. Many factors are within your control, but some will depend on your metal manufacturing partner.
Reduce Inventory And Forecast Smarter
Minimizing your inventory helps you increase cost savings. Lean manufacturing techniques, which aim to eliminate waste while adding value, are effective as you work toward inventory reduction. You also must move materials through the supply chain quickly. Your supplier is able to help by being flexible to your demands and meeting required lead times.
Lowering your level of safety stock is the easiest strategy to reduce inventory. However, this leaves you vulnerable to supply chain disruptions. If inclement weather, unplanned machine downtime or other factors bring the production of just one part to a stop, your whole OEM production line is affected.
Companies with high demand may be able to work with a supplier that holds extra inventory for them to mitigate risk. Extra stock should be stored at your partner’s facility and only invoiced on shipment. By working with such a supplier, you benefit in the following ways:
- Your supplier quickly replaces occasional parts that don’t meet specifications (although defects should be rare)
- Inventory doesn’t take up space at your facility
- You don’t need to ensure extra stock
- Parts can be shipped on a day’s notice when your demand increases
You should also count on your supplier to assist with product forecasting. If you send forecasts, your partner may be able to see variances and catch mistakes that aren’t visible to you. You’re able to meet demand quicker, preventing lost sales, when your product forecasting is accurate. You also prevent excess stock by ordering only as much as you need.
An inventory-focused supplier is a valuable part of your manufacturing supply chain. While it can’t control every variable, it should practice expert parts inventory management to sustain your OEM production and efficiency. The right metal manufacturer will freely discuss its inventory strategies and its role in your OEM supply chain as you consider working together.
Learn how Miller could help improve your business by scheduling a consultation today.