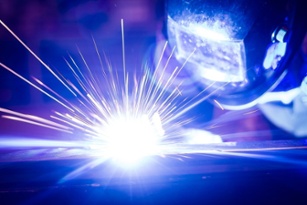
3 Metal Welding Solutions That Drive Substantial Cost Savings
May 6, 2016
Are metal welding costs eating away at your budget? Perhaps your supplier isn’t doing everything in its power to optimize its welding processes and find ways to minimize your expenses.
Your end product’s structure and safety depends on the strength of your welds. Plus, welding defects result in additional costs for your business. Without ever sacrificing quality, your supplier should offer the following three welding solutions to drive down your costs.
1. Perfect The Subtleties And Science Of Welding
Welding is truly a science. The order in which your supplier applies welds affects the quality of your finished parts. Heating a metal causes it to move, shrink and distort. If your supplier controls the distortion, it controls how your finished part comes out.
Suppliers can actually assemble components “incorrectly,” knowing that the welding process will change certain features, and end up with a correct assembly. In other words, if a welder knows something’s going to move an inch after welding, he compensates by moving it an inch the opposite way prior to welding.
Thanks to your supplier’s expertise, you receive higher-quality parts and fewer welding defects that would otherwise slow down your production line. Your customers also make fewer warranty claims because your welded parts are precise.
2. Optimize Welding With Other Manufacturing Processes
OEMs rarely turn to welding contractors for metal welding services alone. They usually want their metal manufacturer to supply material and fabrications as well. In other common scenarios, OEMs request specialty welding, machining and painting services together.
Suppliers should use their scientific knowledge to streamline welding with other manufacturing services. For example, a part that needs post-weld machining using a large piece of equipment with a high hourly rate sometimes can be optimized.
If the feature that needs to be machined is small, your supplier may choose to machine the component (as opposed to the whole part) on a smaller, less expensive machine before welding.
However, it must be pre-machined in a way that compensates for how welding will change and distort the part. You save money by using less expensive machining equipment if your welding contractor’s plan is successful.
3. Minimize Welding Equipment Downtime
Wasted time is expensive for you and your supplier. The two most effective ways for a supplier to reduce welding equipment downtime are to use the appropriate filler metal packages and to schedule downtime for machine maintenance.
Filler Metal Packages
Your supplier should use filler metal packages that are large enough to reduce wire changeovers. However, the packages should not have so much excess wire that they can’t be used within a few days. Once the package is opened, the filler metal absorbs moisture and contaminants like dust and oil, which negatively impact welding processes.
Scheduled Machine Downtime
Scheduled time for maintenance prevents equipment failure. It also ensures higher-quality parts with better equipment performance. Your supplier is able to offer more efficient welding services at a better cost by reducing machine downtime.
Your welding contractor should make your budget goals its focal point. The right partner for your business continuously improves its processes, supporting your growth by working with you to minimize costs as your needs change.
Ready to learn more about how Miller could help you cut costs? Schedule a consultation today.