Coating/Finishing
Polish and Protect Your OEM Parts with Metal Finishing Services
If your heavy equipment is top-of-the-line in functionality, why not ensure that their parts look the part? While metal finishing services can sometimes feel like an afterthought, it’s a process that makes your metal parts last longer and perform better.
Whether you’re looking for a powder or a liquid finish, Miller Fabrication Solutions has the equipment and expertise to meet your custom metal finishing needs. We can match a wide variety of colors, hues and textures and can work with you to make your vision a reality. Take quality to the next level with Miller.
Powder-Coated Parts
Powder coating uses an electrostatic charge application process to bond a mix of additives, pigments and resins to a metal, providing a protective layer between metals and the elements to help stave off rusting and the effects of corrosion. It can also last for up to 20 years.
While our powder coating customers come to us from a range of industries, we often work with forestry and construction equipment manufacturers, due to powder coating’s durability in the outdoors and wear in the field.
Miller Fabrication Solutions’ automated powder coat line is ready to handle your most specific and complex powder-coating challenges. In 2014, we took steps to keep up with the demands of today’s OEMs by purchasing two Nordson 22,000 CFM ColorMax systems. One of the systems has two painting robots with dual Encore HD guns and a 2.8 meter reach. These robots can apply a high volume of powder at relatively low velocities, greatly reducing cycle time. The second system also holds 12 Encore automatic guns. These systems are designed to allow us to coat and protect some of the largest and heaviest parts in our industry. Our automated system can fit parts with dimensions up to 60 inches in width, 72 inches in height and 144 inches in length, and hold a maximum weight of 5,000 pounds. Looking for powder coat finishing services on an even larger part? We also have manual powder coating capabilities for a greater range of sizes.
In all, our paint line includes:
- Blast room
- Five-stage wash
- Powder room
- Dry-off oven
- Curing oven
At each step of the process, your part is looked after by a team of highly-skilled employees. We use a bar code reader for part identification, so that we can track and monitor the flow of every component in the finishing process. At Miller, we run our facility as efficiently as possible to meet and exceed the demand of our heavy equipment manufacturing customers for the timely delivery of high-quality parts.
Everything about our powder coating finishing processes is designed to complete your parts manufacturing. Our dual automated and manual systems allow us to meet your customized powder coating needs.
Wet Coating Treatment
If you’re looking for a fabricated part that’s made of metal not intended for the heat of a curing oven, our meticulous wet coating solutions may be the answer. Metal liquid coating offers great protection against the elements, along with other types of hazards like scratches. It also gives you the capability to have your finish be a thinner layer than is possible with powder coating, for an automotive-quality looking finish.
Miller Fabrication Solutions’ facilities include state-of-the art manual blast, primer and finishing booths. Each booth measures 10 feet 3 inches wide, 13 feet 10 inches high and 80 feet long. Just as with our powder-coating solutions, our metal liquid coating system is specially designed to handle some of the largest and heaviest parts in the equipment manufacturing industry.
Customized to Meet Your Vision
At Miller Fabrication Solutions, we recognize that every one of our OEM customers have specific, unique requirements to make their parts work at the highest level. That’s why we designed both our powder and wet coating solutions to allow you to customize the mil thickness, colors, hues and textures for your metal part finishing.
We use colors from RAL Color Standard and Pantone (PMS), as well as other sources, to ensure that we are able to match your exact specifications. Color changes are performed using an Encore HD Exel feed center for automated powder coating solutions. In all, Miller has worked with over 30 colors and typically does between five and ten color changes per shift.
Powder-part finishing can range in thickness from 2 to 6 mils, while our wet coating solutions can be far thinner. We can work with you if your parts fall outside of our standard ranges. Everything about our process is customized to ensure your project scope is executed exactly.
Throughout each step of our metal finishing services, from preparation to drying, we’re dedicated to upholding the highest level of quality for which we’re known. In fact, over 57% of our customers surveyed rated the total value of solutions provided by Miller as “Excellent” and “Above Average,” according to our 2019 Customer Satisfaction Survey. We recognize that paying for metal finishing is an investment in your product to keep it functioning for longer while fulfilling your brand promise. We strive to honor that investment with work that will withstand the elements and wear for years to come.
If you already depend on us for any of the many other metal fabrication solutions that we offer, then you know that our attention to detail, matched with our ability to meet your lead times, is second to none. Adding our metal finishing services to the work that we already do for you can help you to consolidate your suppliers and allow your supply chain to run smoother than ever.
If you’ve never experienced working with Miller Fabrication Solutions, schedule a consultation with us today to learn more about all of the solutions that we can offer your equipment manufacturing company. We’re here to make your next project a success.
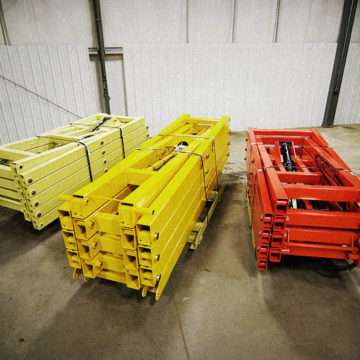